Black Bird
High Powered Model Rocket (2019)
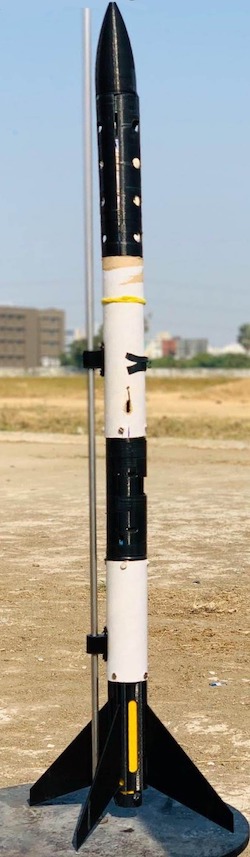
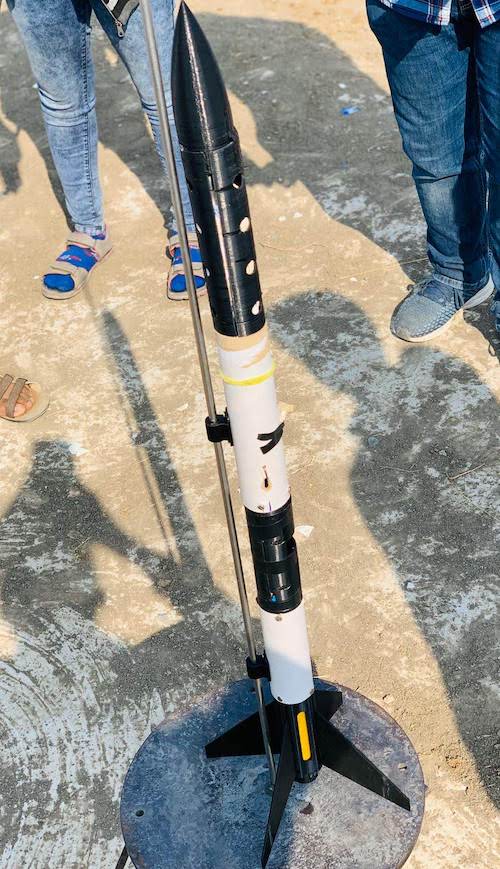
This project was undertaken during Winter Internship 2019 at Avionics Lab, Space Technology and Rocketry (STAR), Surat, India
Project Mission:
To design and develop a High Powered Model Rocket. This Rocket shall reach a minimum height of 120 meters Propulsively and shall have a Recovery System to land on the ground safely.
A Team comprising 9 interns worked on different aspects of the Rocket, namely 2 interns worked on the Design, 2 interns worked on Avionics, 2 interns worked on Recovery System and 3 interns worked on Propulsion.
My Role:
- Member of Avionics Team, I was responsible for the developing Avionics system onboard the rocket to trigger recovery system and collect data.
- Designed General Circuit Board (GCB) based on the dimensions of the rocket, the board had a microcontroller, sensors and data storage devices. The build process included the following steps:
- Roughly Planning the Positioning of various components on paper based on their proximity to the Microcontroller.
- Designing the Circuit by Computer-Aid using Eagle software.
- Realising the actual design on General Circuit Board by Soldering various components on the board and making required connections between the components.
- Various tests were conducted on the GCB before the actual flight.
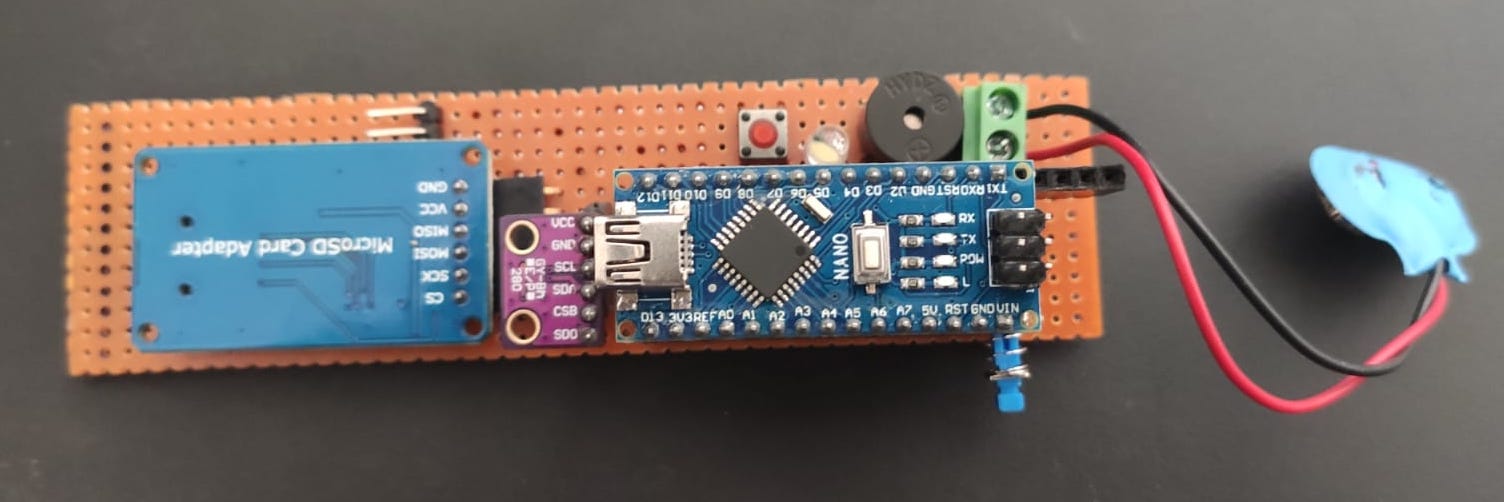
- Developed the software for the GCB.
- The software was capable of Triggering the Recovery Mechanism based on pre-determined conditions using data from the Inertial Measurement Unit and Altitude Sensor.
- The software also recorded data from various sensors and in-flight events.
- Developed Rocket Launch Igniter including the hardware and software.
- The Igniter provided the ability to remotely trigger the launch sequence to light the Rocket Motor.
- The Igniter could be used with Bluetooth or Internet to trigger launch countdown and emergency abort of countdown in case of an anomaly.
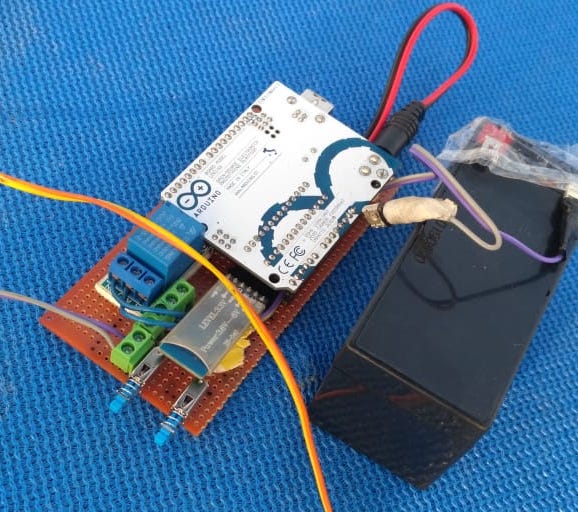
- Developed Android Application to communicate with the Rocket Launch Igniter.
- The application provided the ability to initiate the launch countdown and emergency abort the countdown in case of anomaly.
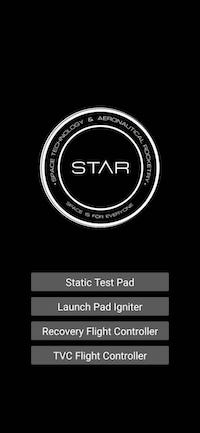
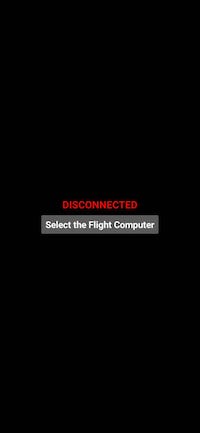
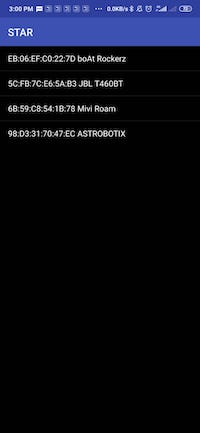
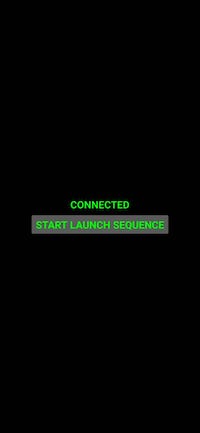
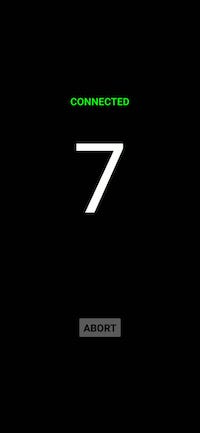
From left to right: Start Screen, Launch Pad Igniter interface, Bluetooth Selection Menu, Launch Sequence Starter interface, and Interface during launch sequence showing countdown and abort options.
- Developed Static Launch Test Pad to help Propulsion Team test different motors.
- Static Launch Pad used a load cell to measure the thrust and burn-time of the motor.
- The data recorded was used by Propulsion Team to analyse different fuel compositions for the rocket motor.
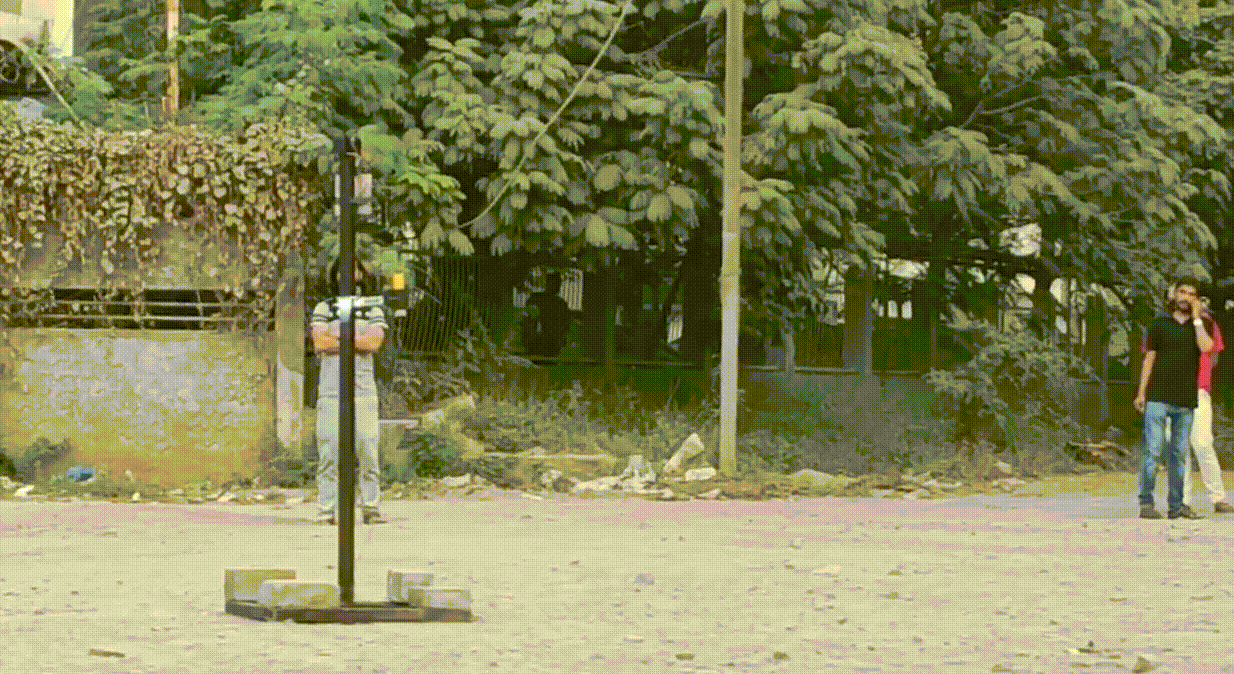
Testing of the rocket motor on the static launch pad. A load cell is used to characterize the thrust curve.
Project Accomplishments:
- 2 High Powered Model Rockets were successfully developed.
- A Remote Launch Igniter and a Static Test Pad was also developed.
- Many integrated tests were conducted of all the Systems:
- Numerous ground tests were conducted for the main Rocket Avionics Board and Wireless Igniter.
- 10+ Drop Tests were conducted for the main rocket avionics GCB.
- 9 Static Tests were conducted and data collected was analysed to determine the composition of fuel for the motor.
- 2 Rocket launches were conducted with all systems together.
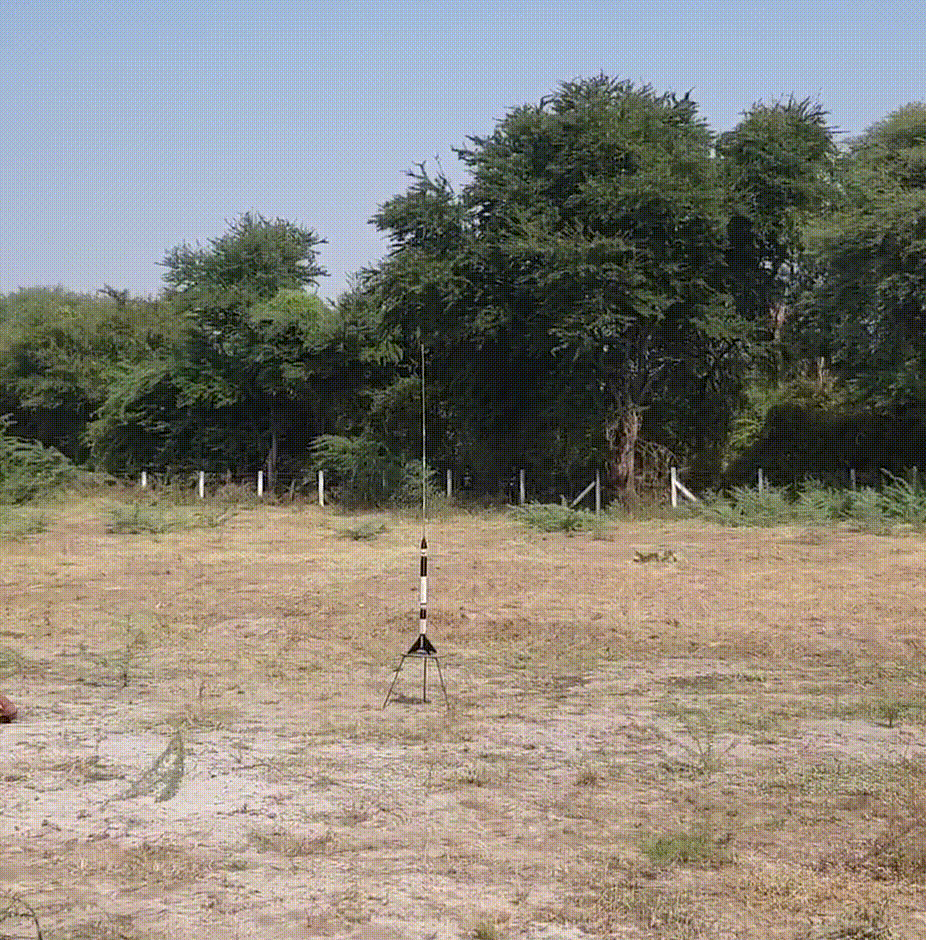
Successful launch of our model rocket, demonstrating the culmination of our team's efforts in rocket design, propulsion, and avionics systems!